Locusview has been working with a Tier 1 electric and gas utility to digitize their utility construction and as-builting workflow with Locusview’s Digital Construction Management (DCM) solution. The utility has been managing their gas construction workflows using Locusview since 2019 providing benefits including improved ability to respond to manufacturer recalls and GIS viewer updates within 24 hours.
In December 2023, the utility deployed Locusview for their electric as-builting workflows to streamline their GIS clearance process, provide timely and accurate asset data to their electric GIS system of record and better support their grid modernization programs and ADMS. With this deployment the utility now uses Locusview’s DCM solution to manage all electric and gas construction activities across eight states to improve safety, service and reliability to their 1.33 million electric and gas customers.
Legacy Workflow
The utility’s electric construction workflows were previously managed with a combination of paper and legacy GPS hardware. The workflow (shown below) involved delivery of a paper job packet to the field for construction prints and as-built data collection. There was no real-time visibility of project progress or status to the GIS team. Paper as-builts were then delivered to the GIS team weeks to months after construction was completed delaying downstream GIS data use such as EAM and ADMS. The GIS team was ultimately responsible for capturing electric as-built asset data for the utility’s GIS system of record during their ”GIS clearance work”. The workflow included two separate field visits to capture electric construction as-built data:
- One visit by the construction crew to perform installation and collect as-built data using a paper job packet
- A second visit by the GIS team to perform “clearance work” consisting of capturing GPS locations and attributes of installed electric assets
The output of the clearance work was a .CSV file exported from the GPS devices that represented the actual GPS locations of as-built assets. The data required tedious post-processing to create asset representations from raw GPS coordinate data - e.g. individual vertices for each line had to be merged together to form the line route for the given asset (underground cable, ducts, trench, road centerline, etc.). The .CSV file was then imported into the GIS system of record using an existing custom import routine. GPS reference lines and points were displayed as separate layers and used to “as-built” the proposed design by manually moving designed asset locations from the graphic work design (GWD) to the GPS location of the constructed asset captured during clearance work. When done, the work order was manually closed out in the utility’s other systems of record:
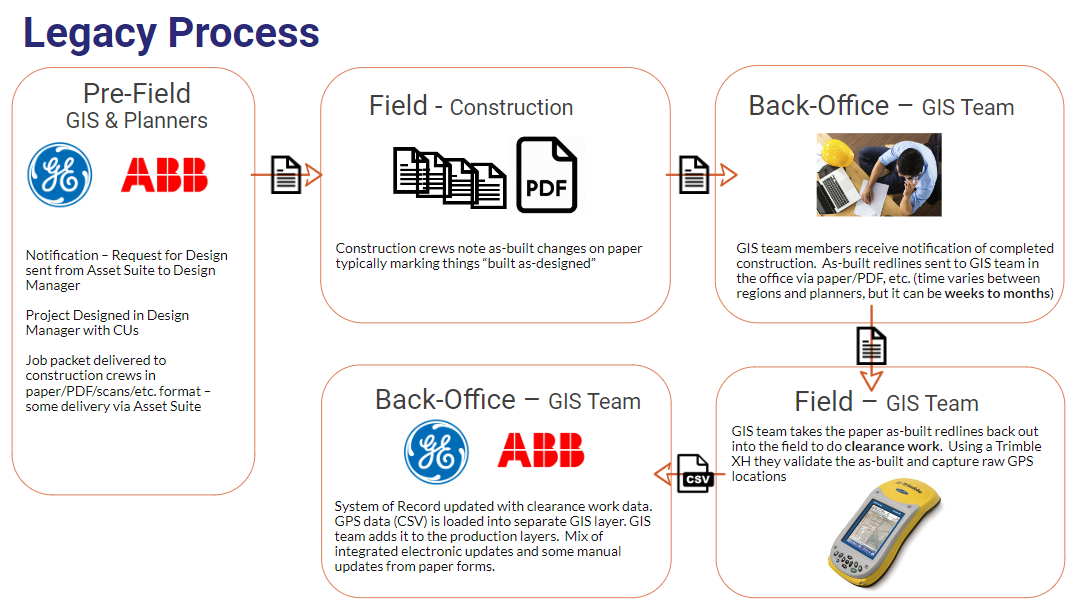
New Workflow
In the new workflow using Locusview, the utility construction crews continue to deliver construction data to the GIS team in their current as-is workflow. The GIS team then creates a digital work order in Locusview’s web application and attaches pertinent documents needed for their clearance work resulting in a Digital Job Packet. The GIS teams plan, manage, organize and prepare for their field visits using Locusview’s web-based Project Management module. In the field the GIS team performs their clearance work using the Locusview mobile application on iPad Pros integrated with Trimble Catalyst GPS units. Forms tailored to the utility’s data collection workflows are used to capture attribute data for constructed electric assets and landbase features. The integration to the Trimble Catalyst GPS device allows crews to easily capture all electric distribution asset locations as well as road centerline routes with survey-grade accuracy. The utility can also use Locusview to capture data for Map Updates and Unplanned Work job types as well as any customer interactions that take place. Alerts notify users of data conditions such as inadequate GPS accuracy, missing data values or assets that were not mapped.
When field data collection is completed, validated, reviewed and approved, the Locusview system automatically exports as-built data and generates as-built reports. Data is delivered in a format that is ready to be used with the utility’s current GIS import process eliminating the legacy data post-processing step . The new workflow is shown below:
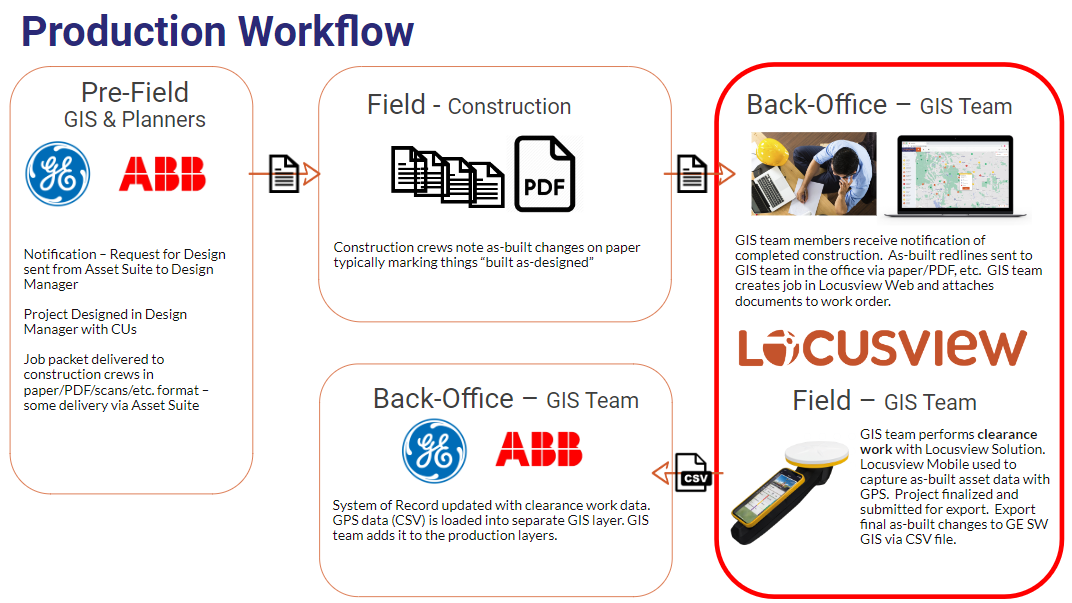
Project Approach
Locusview’s DCM solution has capabilities to fully digitize and optimize the utility’s entire workflow and reduce it to a single field visit by using existing construction crews to perform digital as-builting and GIS clearance work simultaneously (as many of Locusview’s other customers do daily). However, the utility’s goal was to focus on the GIS clearance process and chose to deploy Locusview’s platform through a two-phased approach to minimize change management and speed time to value. Phase 1 was a field Pilot focused on GIS clearance work. Phase 2 was a Production Deployment that operationalized the Pilot’s approach and deployed it to the field.
Project success Criteria included:
- Match or improve the existing workflow and data deliverable to update the utility’s GIS
- Replace legacy GPS devices with Locusview & Trimble Catalyst for electric clearance work
- Match or improve the user experience for field data capture through Locusview Mobile user interface
- Improved data capture quality with Locusview field validation
Phase 1 enabled the utility to experience the benefit of Locusview’s technology and prove out the value in a short timeframe (~3 months). The Pilot focused on incrementally improving this workflow by only replacing the GIS team’s GPS solution with Locusview’s solution. The Pilot was successfully deployed during the COVID-19 pandemic. Locusview’s cloud architecture and SaaS platform provided innovative ways to deliver the Pilot through a combination of remote virtual configuration and training sessions as well as on-site visits when they were permitted.
After the successful Phase 1 Pilot, Locusview worked with the utility to deliver Phase 2 - a full production electric as-builting project. Phase 2 built off of, enhanced and operationalized the Pilot’s approach and included configuration improvements based on user feedback, finalization of the workflows, and automated generation of reports and as-built data exports. The project also expanded use to all of the utility’s GIS-clearance crews in three states. Locusview also implemented an integration to the utility’s GIS system of record and deployed a Trimble Catalyst GNSS hand-held form factor to capture high-accuracy GPS asset locations. Overall, the project provided change management, customer readiness, product enhancements and training and provisioning all in under 5 months.
Solution Capabilities
The Locusview solution capabilities implemented include:
1. Configured Work Types
- Electric Distribution As-builting - Clearance
- Map Update - Unplanned work
2. Digital Forms
3. GPS Field Asset capture
4. Quality Assurance/Quality Check
- Mobile data alerts
- GPS Accuracy Alerts
5. PDF Reports
- Standard Form Reports
- Custom downloadable As-Built report
6. Integrations and Data Transfer
- GIS
7. Customer SAML User Authentication through Microsoft Azure SSO
8. Locusview Turnkey Package (see photos)
- iPad Pros (utility provided)
- Trimble DA2 GNSS receiver
- Trimble Catalyst Handle, battery and magnetic mount
- Trimble Catalyst 60 GNSS positioning service subscription
- Locusview Electric kit and case
- LocusviewBUILD software
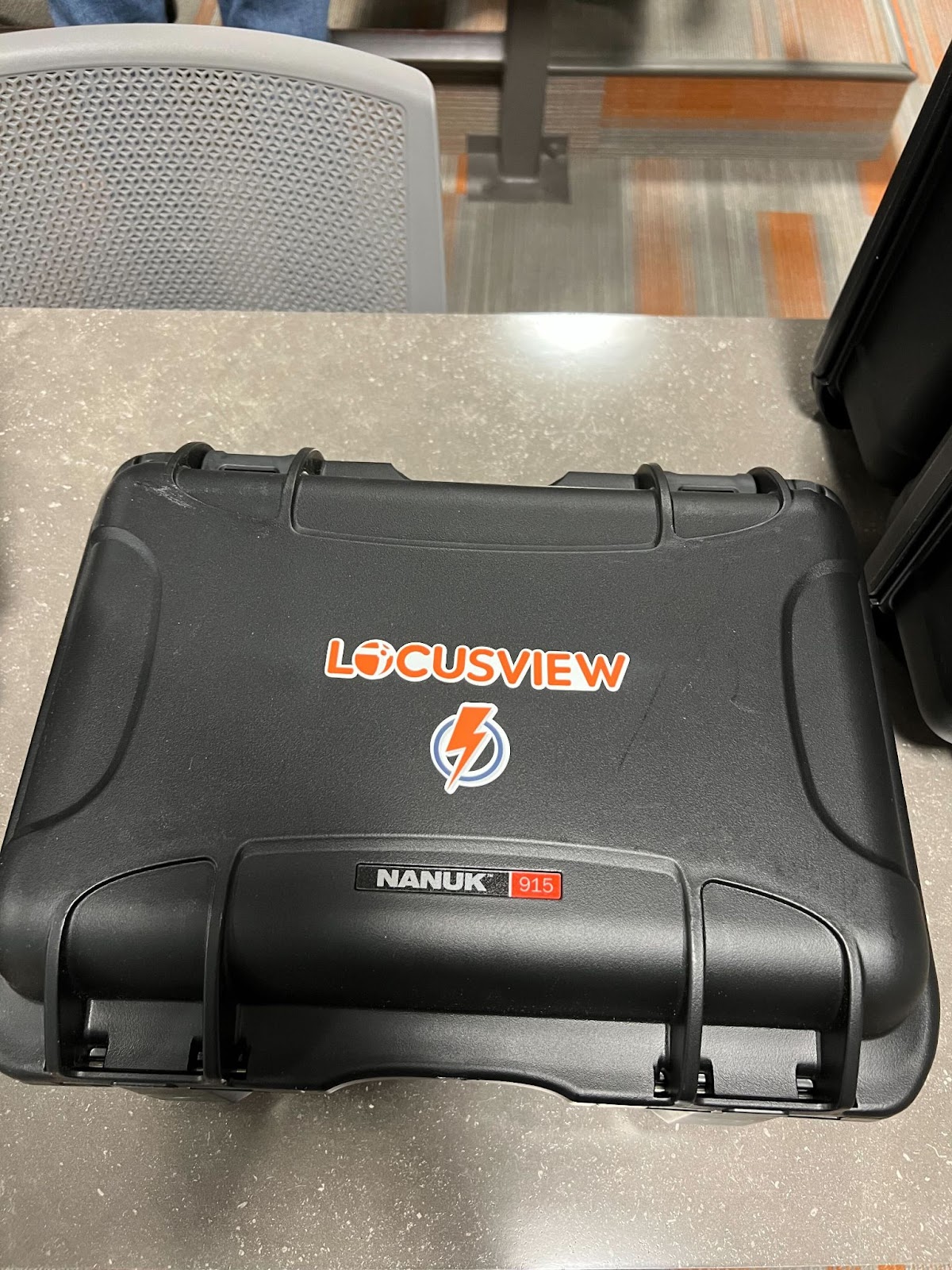
Photo - Locusview electric digital as-builting kit
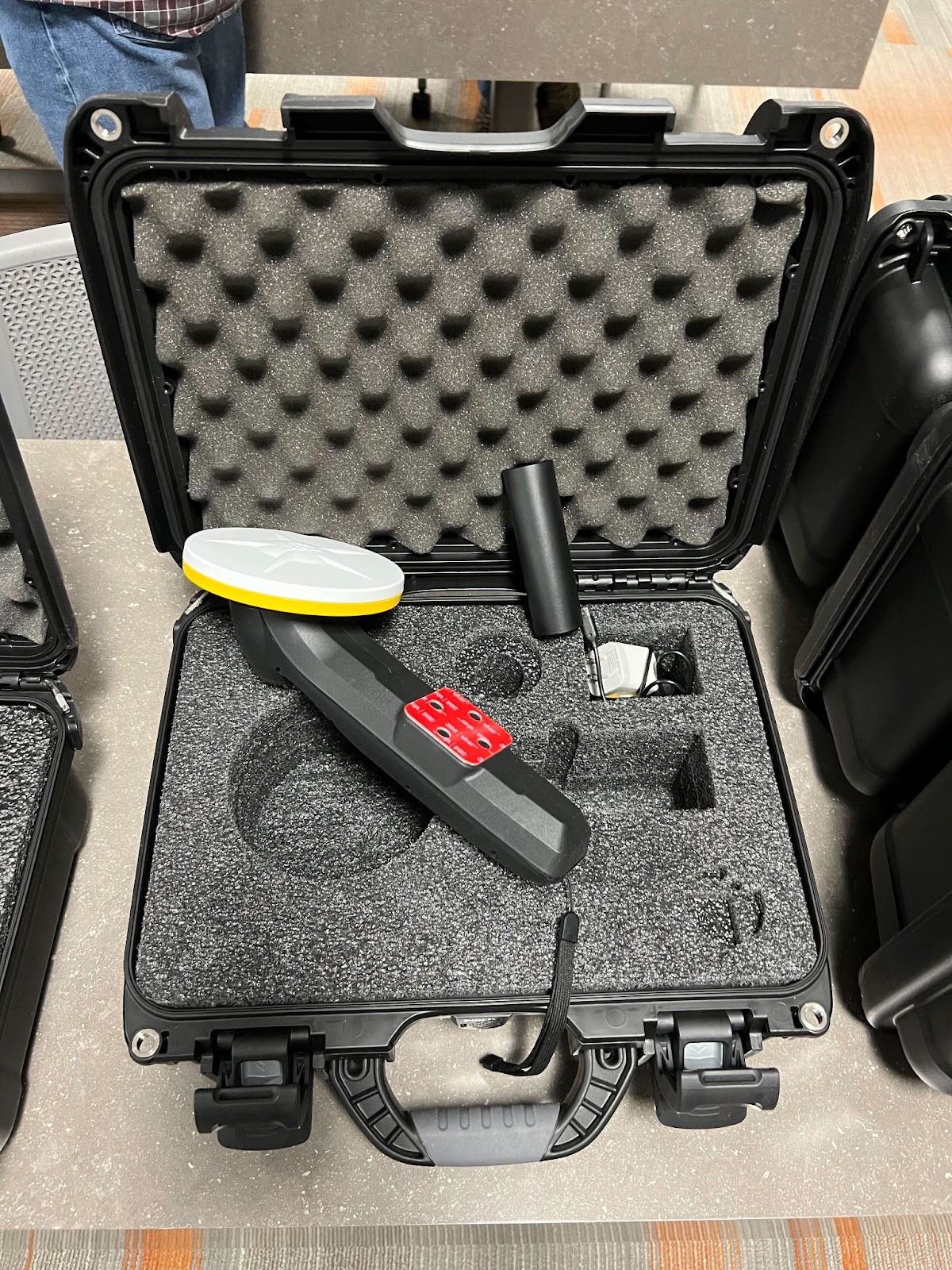
Photo - Details of the Locusview electric digital as-builting kit
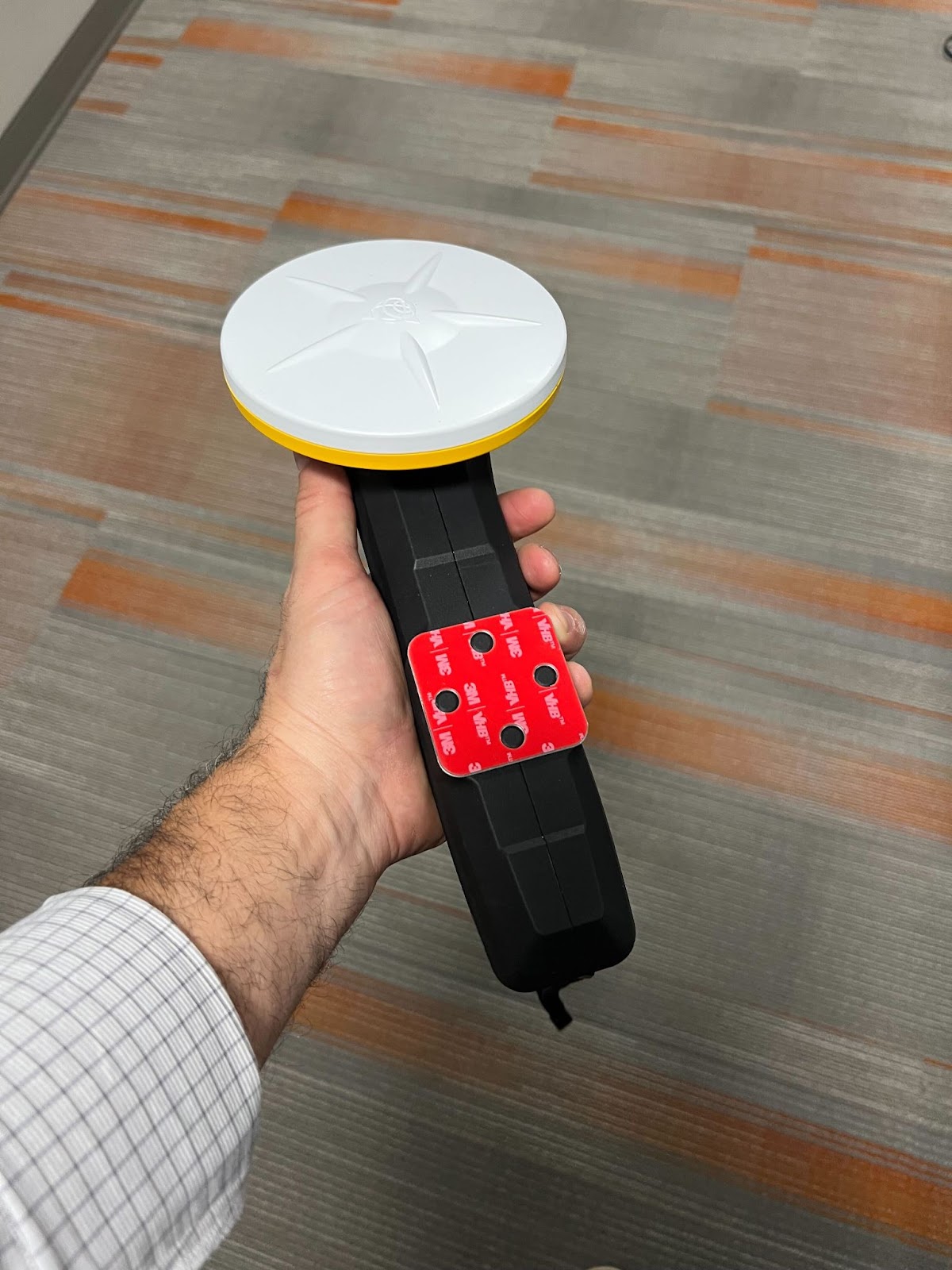
Photo - Trimble Catalyst hand-held GNSS solution